Different Types of Metal Finishing Chemicals
- CVD Coating
- Jan 18, 2019
- 2 min read
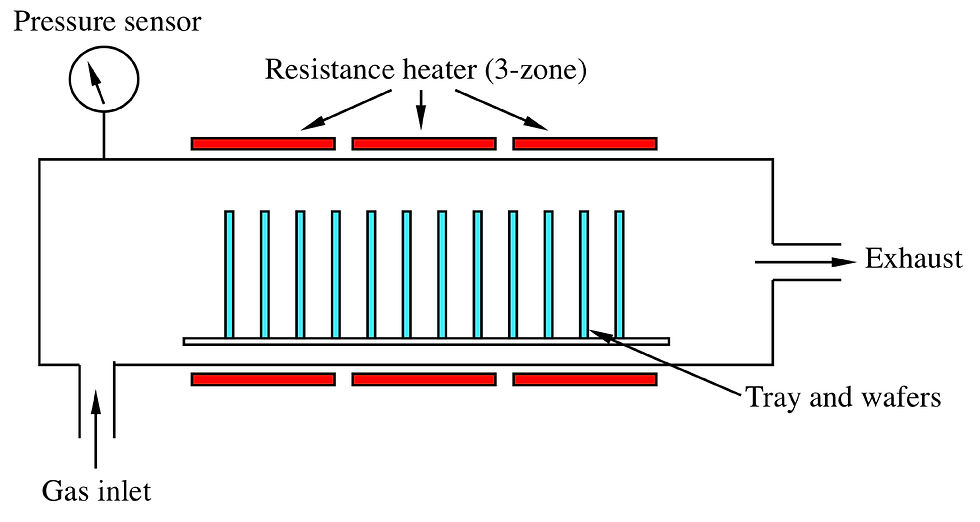
Metal finishing alters the surface of metal products to enhance corrosion resistance, wear resistance, electrical conductivity, electrical resistance, reflectivity and appearance, torque tolerance, solder ability, Tarnish resistance, chemical resistance, and hardness. Electrolytic plating, electro less plating, and chemical & electrochemical conversion processes are typically used in the industry.
Types of metal finishing processes are electroplating, electro less plating, chemical and electrochemical conversion, cladding, and case hardening, dip/galvanized coatings, electro polishing, and vapor deposition. Chicago metal finishing chemicals serves industries like automotive, agriculture, office furniture, appliance, off-road, coil coating, lawn and garden, aerospace, outdoor furniture, lighting, industrial racking, bearings, remanufacturing, custom coaters, air distribution, recreational, military, plating, medical equipment, and processing equipment.
Metal finishing can be categorized into electroplating, metal blackening, black oxide, corrosion inhibitors, metal cleaners, metal bright dips, surface preparations, phosphate finishes, waste treatment chemicals, chromate conversion etc. A corrosion inhibitor is a chemical compound that, when added to a fluid or gas, decreases the corrosion rate of a metal or an alloy. Some of the corrosion inhibitors are hexamine, phenylenediamine, dimethylethanolamine, sodium nitrite, and cinnamaldehyde.
Electro less plating is a method of depositing a transitional metal on to a metallic substrate using a process of chemical reduction. Electro less plating is used for coating nonmetallic parts. The area where electro less plating are oil & gas, plastics, textiles, automotive, aviation & aerospace, food & pharmaceutical and Chemical processing.
In aerospace it is used in rams pistons, valve components, and satellite and rocket components. In automotive it is used in shock absorbers, heat sinks, gears, cylinders, brake pistons etc. Black oxide is unlike any other finish. Black oxide is a conversion coating formed by a chemical reaction produced when parts are immersed in the alkaline aqueous salt solution operated at approximately 285 degrees F. advantages of black oxide are no dimensional changes, dark black color, reduces light glare, improved lubrication characteristics, color change resistant to temperature, no white corrosion, weld able and no hydrogen embrittlement. Bright dip can be used to finish copper, brass, and even stainless steel. Black metal is a heavy metal. It is often used in fast tempos, shrieked vocals; highly distorted guitars played with tremolo picking, double kick drumming and unconventional song structure.
There are two general types of black oxide for iron and steel are hot black oxide and room temperature blackening. Surface preparation implies that an existing surface must be prepared prior to the installation or application of a new surface. Surface preparation is a two stage process - removal and profiling. Popular removal equipment are strippers, shot blasters, grinders, scrapers scarifies and planers. This can be used in carpet, ceramic title, wood, rubber, linoleum, epoxies, non-skids, paint, stains and adhesive surface.
Comments